Engine Boring for Best and Smooth Rings Surface
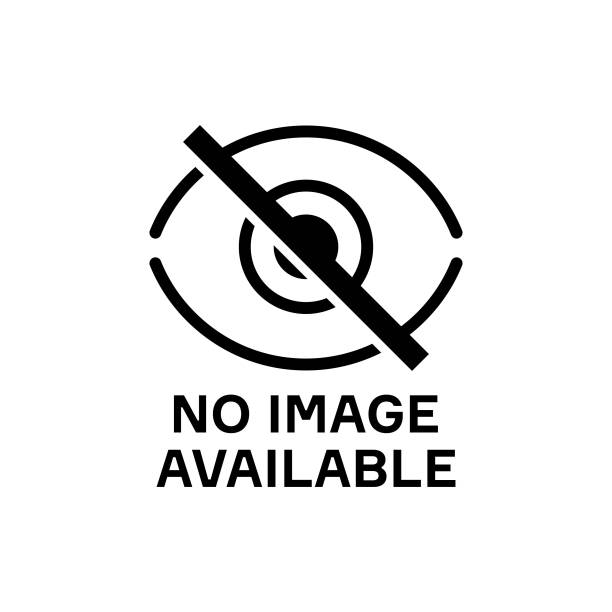
February 16, 2017
Achieve the OEM levels of smooth engine ring surface by doing Engine Boring with Grit diamond honing stone
Whenever an engine is reconditioned or rebuild, there are some parts that also require some attention. Due to some wear and tear in the engine, taper create at the upper part of the cylinder that can minimize the pressure of ring sealing and increase oil consumption if it is not removed. To understand the purpose of refining the engine cylinders is to make the cylinder walls as straight as possible and the engine cylinder bores as round as possible to get the best amount of crosshatch for good oil retention and ring support. This all can be done by engine boring or honing the cylinders. There are only two ways to increase an engine’s displacement, either bore it or stroke it. Engine boring always tends to increase the cylinder diameters whereas the engine stroking increases the crankshaft stroke.Simple to Understand Engine Bore
To understand how the engine bore is done, engine bore specialists use special equipment to smooth out the surface of scratched, scored or excessively worn engine cylinders. What they do is they actually remove a thin layer of metal to within thousandth of an inch of the piston size that will be used to rebuild the blocks.Cylinder Boring Challenges
Most of the aftermarket engine rebuilders may not have the know-how or exact knowledge of honing equipment to reproduce an OEM type of cylinder bore finish. The biggest challenge for the engine rebuilders is that to do engine boring in such a way that fulfils the OEM bore finish.Good Cylinder Bore Finish
There is a recommended bore finish for the rings which is done by all engine boring mechanics. It would be 28 to 35 RA. RA is the roughness average in micro inches. The engine boring equipment is known as grit stone which has the size of A#280. It is usually recommended for moly rings because these rings have smoother finish of 16 to 23 RA. Grit diamond honing stone of 500 to 550 will also be capable of producing a surface finish in the 13 to 15 RA range.Categories
- Reconditioned Engines
- Land Rover
- BMW
- Saloon
- Mitsubishi
- Jaguar
- Infotainment System
- Mitsubishi
- Ford
- Fiat Ducato
- Ford Mondeo
- Citroen
- Mazda
- Ford Ranger
- Peugeot Boxer
- Cylinder Head
- Info-graphics
- Reconditioned Engine
- Engine Pistons
- Blown Head Gasket
- Engine Boring
- Engine Replacement
- Machine Shop
- Engine Surface Treatment
- Crankshaft Bearing Coatings
- Engine Degreasing
- Connecting Rod Crack
- Engine Connecting Rods
- Engine Valve Grinding
- Engine Block Liners
- Crankshaft Crack
- Crankshaft Polishing
- Crankshaft Balancing
- Crankshaft Grinding
- Nissan
- Valve Lapping